Jika anda sedang mencari What Is Motor Dc And Rotary Encoder, anda berada di tempat yang tepat! Disini saya akan mencoba membahas beberapa pertanyaan mengenai What Is Motor Dc And Rotary Encoder.
What is rotary encoder?
Rotary Encoders are sensors that detect position and speed by converting rotational mechanical displacements into electrical signals and processing those signals. Sensors that detect mechanical displacement for straight lines are referred to as Linear Encoders.
How does a motor encoder work?
Encoders convert motion to an electrical signal that can be read by some type of control device in a motion control system, such as a counter or PLC. The encoder sends a feedback signal that can be used to determine position, count, speed, or direction.
Why are encoders used with motors?
Encoders are used in devices that need to operate in high speed and with high accuracy. The method of controlling the motor rotation by detecting the motor rotation speed and rotation angle using an encoder is called feedback control (closed loop method).
What are the types of encoder?
An encoder is classified into four types: mechanical, optical, magnetic, and electromagnetic induction types. There are four types of information necessary to rotate the motor with high accuracy: rotation amount, rotational speed, rotational direction, and rotational position.
What encoder means?
Encoder definition In general an encoder is a device or process that converts data from one format to another. In position sensing, an encoder is a device which can detect and convert mechanical motion to an analog or digital coded output signal.
What are the application of encoder?
An encoder is a device, algorithm, that is a software program or person that converts the information from one format or code to another. The main purpose of the encoder is standardization, security, speed or saving space by shrinking size.
How does encoder measure speed?
Encoder speed can be determined by either of two methods: pulse counting or pulse timing. Incremental encoders often output signals on two channels – typically termed “A” and “B” – offset by 90 degrees (in quadrature). The direction of rotation can be determined by which channel is leading.
What is encoder circuit?
An Encoder is a combinational circuit that performs the reverse operation of Decoder. It has maximum of 2n input lines and ‘n’ output lines. It will produce a binary code equivalent to the input, which is active High. Therefore, the encoder encodes 2n input lines with ‘n’ bits.
What is an encoder job?
An encoder is a data entry professional who helps organize and maintain information for their employer. As an encoder, you can find work at a variety of places, such as a healthcare facility, financial institution, or corporate office.
What type of device is an encoder?
Encoders are devices that receive as input an uncompressed data stream (video and/or audio), encode the stream into a specific format, such as MPEG2, and then output an encoded stream. Encoder devices may be a part of another device, such as a combination TV tuner/capture adapter, or they may be separate.
Are encoders digital or analog?
Encoders (AKA Analog vs. Digital) Because of the way they operate, potentiometers are an inherently analog input device, while encoders are digital.
What is BCD encoder?
In computing and electronic systems, binary-coded decimal (BCD) is a class of binary encodings of decimal numbers where each digit is represented by a fixed number of bits, usually four or eight.
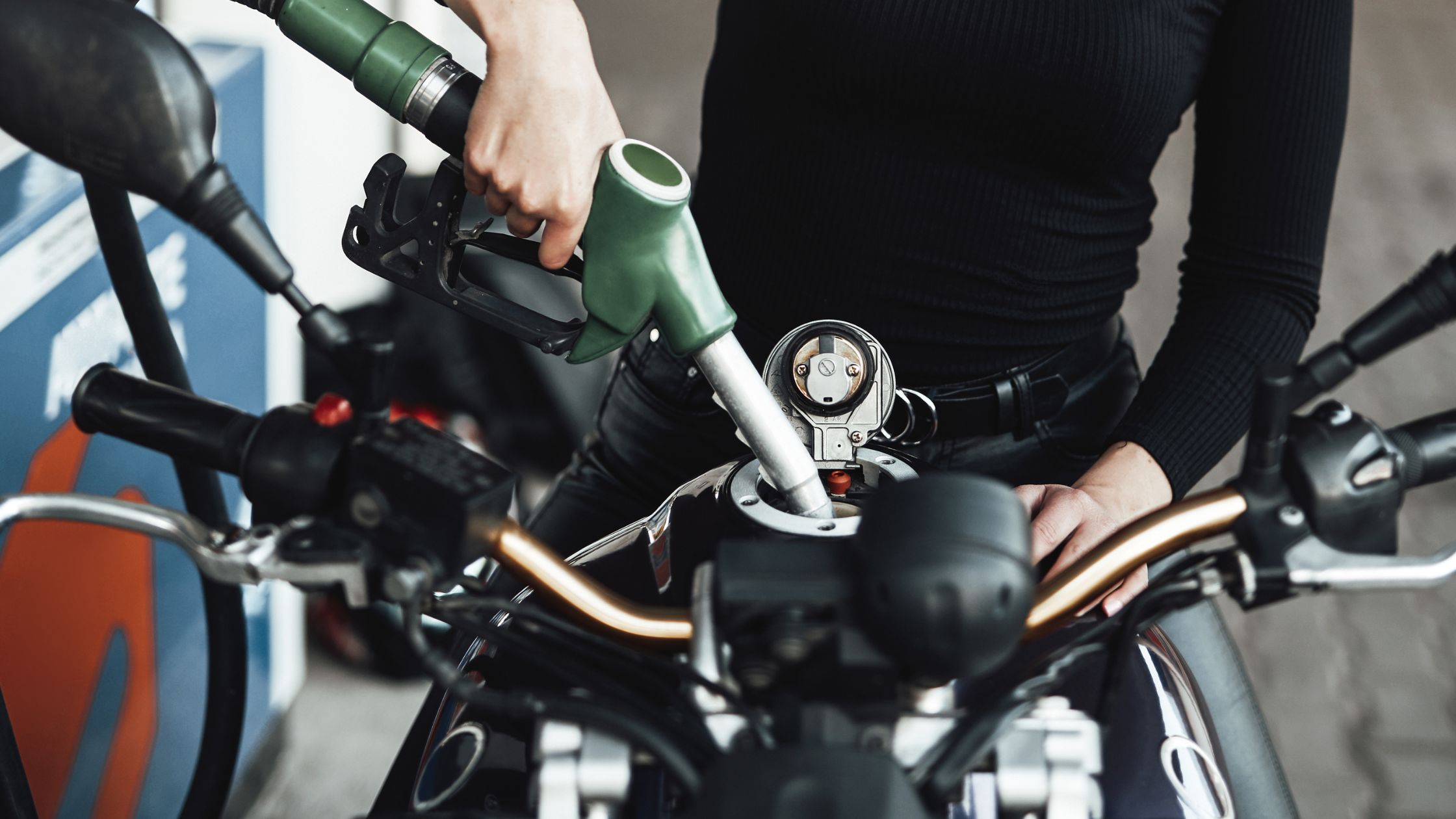
How many pins does a rotary encoder have?
Rotary Encoder with Switch With a total of 5 pins, 3 on one side for rotary encoding which need a simple circuit to supply DC 5V while the other two go short whenever pressed, you’re not short of any functionality when using this!
What is a DC motor driver?
DC motor drives are defined as amplifiers or power modules that interface between a controller and a DC motor. They convert step and direction input from the controller to currents and voltages compatible with the motor.
Do DC motors need drivers?
Motor-driven Main Components For the dc motor, you need a controller, motor driver circuit, DC motor, power supply unit, and the necessary direct connections. This controller can be a microcontroller or a microprocessor.
Is a servo motor AC or DC?
Servo motors come in two basic types: AC and DC. Each type is designed for a different range of applications, but both can be found in various industrial and domestic machines and devices.
What is meant by servo motor?
A servo motor is an electromechanical device that produces torque and velocity based on the supplied current and voltage. A servo motor works as part of a closed loop system providing torque and velocity as commanded from a servo controller utilizing a feedback device to close the loop.
Why do encoders fail?
The most common cause of encoder failure is a warped/ bent shaft that is no longer sitting on the bearings properly, an issue also referred to as shaft run-out. A warped shaft adds stress to the internal bearings and may lead to bearing failure and eventual overheating of the encoder.
How do you wire a rotary encoder?
Connect one button switch pin on the rotary encoder to ground on the ItsyBitsy (top black wire). Connect one button switch pin on the rotary encoder to the D12 pin on the ItsyBitsy (green wire). Connect the C (common ground) pin on the rotary encoder to the ground pin on the ItsyBitsy (middle black wire).
Can an encoder be repaired?
Most encoders are easily repairable.
What is the advantage of using an encoder?
Advantages: The biggest advantage of absolute and incremental encoders are that they are inherently digital, which means they can interface easily to modern control systems. An encoder sends digital quality signals back to the computer.
How do you calculate RPM from encoder?
RPM = (Frequency X 60)/ Line Count This will be our frequency, or the number of optical encoder counts that we have accumulated in one second. We then multiply that value by 60, which uses our one second total to convert to the number of pulses occurring in a minute.
How do you calculate motor speed with encoder?
The first half of equation is Distance per 1 pulse = (200/ Number of pulses per rotation) / 1000, the latter half of equation is Number of output pulses/ Time = Number of pulses per minute = Frequency x 60. Then, Speed (m/min) = (200/ Number of pulses per rotation) / 1000) x Frequency x 60.
How is encoder frequency calculated?
Frequency = (RPM X Line Count/60) Use this formula when line count of the encoder and RPM are known. The answer is in Hertz (Hz) or cycles per second. Keep in mind that many encoders and drives will have a maximum frequency limit that you should not exceed.
Terimakasih telah membaca What Is Motor Dc And Rotary Encoder, semoga jawaban dari pertanyaan anda telah saya jawab semua. Semoga bermanfaat!