Jika anda sedang mencari What Is A Pid Dc Motor, anda berada di tempat yang tepat! Disini saya akan mencoba membahas beberapa pertanyaan mengenai What Is A Pid Dc Motor.
What is a PID and what does it do?
A PID controller is an instrument used in industrial control applications to regulate temperature, flow, pressure, speed and other process variables. PID (proportional integral derivative) controllers use a control loop feedback mechanism to control process variables and are the most accurate and stable controller.
Is PID better than pi?
As we can there see is a decrease in rise time, overshoot and settling time and there is no change in steady state error PID Controller is better than P and PI controller.
Is PD controller better than PID?
In terms of speed, PID controller has the fastest response as it shows the fastest time constant of 0.17s and settling time compared to the PD and PI Controllers, however in terms of Damping the PD controller has the best performance because no overshoot was observed at steady state compared to the PI and PID …
What are the benefits of PID control?
PID-control is most commonly used because it combines the advantages of each type of control. This includes a quicker response time because of the P-only control, along with the decreased/zero offset from the combined derivative and integral controllers.
What does PID stand for in electrical?
PID stands for Proportional, Integral, Derivative. PID control provides a continuous variation of output within a control loop feedback mechanism to accurately control the process, removing oscillation and increasing process efficiency.
How can PID be used to control the speed of a DC motor?
The Discrete PID controller is used to measure the Speed, Torque and Voltage of the DC motor and then send it back as feedback. The implementation of the speed block is shown in figure 5. Using this feedback the difference between the set speed and actual speed is slowly removed.
What is PID speed?
PID stands for Proportional Integral Derivative. In a PID Algorithm, the current speed of the motor is measured and compared with the desired speed. The error is used in complex calculations to vary the duty cycle of the Motor with respect to time.
Is PID control the best?
No, PI is not the best controller. It is only the most common controiller, because many, or maybe even most, applications are simple and do not need too much. You just close a loop with some proportional gain P and the closed-loop may happen to already be stable.
When would you use a proportional controller?
Proportional control is used where maintaining a process variable to a tighter tolerance and timely responsiveness are required. Control systems in many industrial settings as well as some smart devices use proportional control. Proportional control involves fine-grained control through a feedback mechanism.
What are disadvantages of PID controller?
It is well-known that PID controllers show poor control performances for an integrating process and a large time delay process. Moreover, it cannot incorporate ramp-type set-point change or slow disturbance. We discuss the above-mentioned limitations of the PID controller.
Where are PID controllers used?
Proportional-Integral-Derivative (PID) controllers are used in most automatic process control applications in industry today to regulate flow, temperature, pressure, level, and many other industrial process variables.
What is P PI and PID?
P, PI, and PID Controllers It determines the deviation of the system and produces the control signal that reduces the deviation to 0 and small value. The manner in which the automatic controller produces the control signal is called the control action.
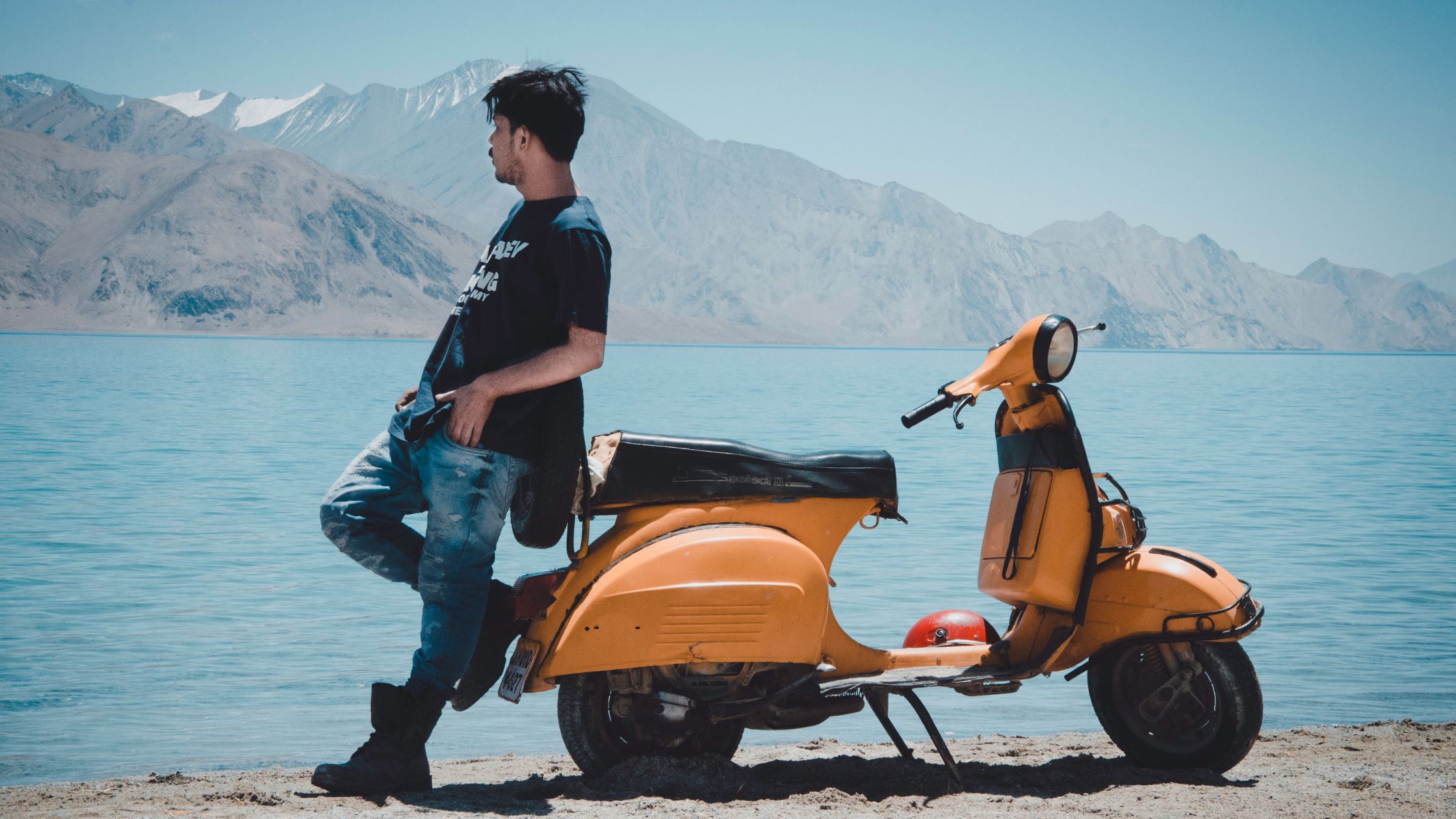
What are the two best advantages of PID control?
The advantage of PID controller is its feasibility and easy to be implemented. The PID gains can be designed based upon the system parameters if they can be achieved or estimated precisely.
Do I need a PID controller?
A PID loop would be necessary only if high precision were required. Otherwise, a thermostatic controller like the one in most homes should be able to maintain a more-or-less constant temperature by simply turning the heater on when the temperature drops too low or off when the temperature rises too high.
Is PID and PLC same?
A PID Controller is different to a PLC. It still requires inputs and outputs to receive information from the process and send signals back to control it but it contains specialist algorithms designed to control a process with one or multiple control loops.
Is Arduino a PID controller?
The second part deals with the designing of our system, an Arduino-based temperature controller system using the PID algorithm. The codes written in C programming serve as the software portion, while the hardware portion includes Arduino UNO, electronic components, and solid state devices.
How do you tune a PID?
Manual PID tuning is done by setting the reset time to its maximum value and the rate to zero and increasing the gain until the loop oscillates at a constant amplitude. (When the response to an error correction occurs quickly a larger gain can be used. If response is slow a relatively small gain is desirable).
How are DC motors controlled?
Thus, the speed of a DC motor can control in three ways: By varying the flux, and by varying the current through field winding. By varying the armature voltage, and the armature resistance. Through the supply voltage.
What is the transfer function of PID controller?
The transfer function of a PID controller is found by taking the Laplace transform of Equation (1). = derivative gain. C = s^2 + s + 1 ———– s Continuous-time transfer function. C = 1 Kp + Ki * — + Kd * s s with Kp = 1, Ki = 1, Kd = 1 Continuous-time PID controller in parallel form.
Where is PID used give example of its application?
A PID controller is an integral part of the temperature control system of an industry. It is typically used to control the temperature of the premises. Here, the input of the PID controller is obtained from a temperature sensor and the output is fed to a fan or a heater.
How does PID controller reduce oscillation?
The PID controller is not stable, or oscillating: Start by decreasing the derivative gain to a low setting (to ensure it is not causing the instability), then decrease the proportional gain until the controller becomes more stable.
What is a PID controller and explain its application with a suitable example?
Temperature Control Using PID Published April 17, 2019. Down. A good example of temperature control using PID would be an application where the controller takes an input from a temperature sensor and has an output that is connected to a control element such as a heater or fan.
When should you not use PID?
If the system has two elements competing against each other, it is a second-order system, and a PID controller likely is not the right solution. For example, a process that includes a heater and a chiller would clash, and the PID controller would not be effective. It could also destroy the system.
Is PID a linear controller?
Since the conventional PID is a linear controller it is efficient only for a limited operating range when applying in nonlinear processes.
Terimakasih telah membaca What Is A Pid Dc Motor, semoga jawaban dari pertanyaan anda telah saya jawab semua. Semoga bermanfaat!