Jika anda sedang mencari How To Make Pwm Dc Motor Speed Controller, anda berada di tempat yang tepat! Disini saya akan mencoba membahas beberapa pertanyaan mengenai How To Make Pwm Dc Motor Speed Controller.
How can PWM be used to control the speed of a DC motor?
In this paper, to control the speed of DC motor using Pulse Width Modulation (PWM) method. Microcontroller AT89S52 is used to generate PWM. L293D IC is used to drive the motor which is made up of two H-Bridge. 555 IC is used with opto coupler to sense the speed of DC motor.
Can you control DC motor with PWM?
There are many different ways to control the speed of DC motors but one very simple and easy way is to use Pulse Width Modulation.
How do you control the speed of a DC motor using PWM Arduino?
When the speed is varied from 1 to 9, the speed increases, with the value 9 set as the maximum speed of the motor. A PWM DC motor controller technology is used to control the speed. In PWM, the Arduino sends a pulsating wave that is similar to astable mode of 555 timer IC.
How do DC motors control speed?
Thus, the speed of a DC motor can control in three ways: By varying the flux, and by varying the current through field winding. By varying the armature voltage, and the armature resistance.
What is best PWM frequency for DC motor?
Choose the frequency that provides the best balance of torque throughout the desired speed range while balancing the motor chatter that can happen at lower frequencies. As a rule of thumb, most small brushed DC motors will operate nicely with a PWM frequency of 50Hz to 100Hz and slow decay mode.
What is the disadvantage of PWM?
Disadvantage of PWM The disadvantages of PWM may be described by under: Due to the variable pulse width, the pulses have variable power contents. Hence, the transmission must be powerful enough to handle the maximum width, pulse, though the average power transmitted can be as low as 50% of this maximum power.
Do DC motors need PWM?
Pulse-width modulation (PWM) or duty-cycle variation methods are commonly used in speed control of DC motors. The duty cycle is defined as the percentage of digital ‘high’ to digital ‘low’ plus digital ‘high’ pulse-width during a PWM period. Fig. 1 shows the 5V pulses with 0% through 50% duty cycle.
How does PWM affect motor speed?
If we switch the power on and off quickly enough, the motor will run at some speed part way between zero and full speed. This is exactly what a p.w.m. controller does: it switches the motor on in a series of pulses. To control the motor speed it varies (modulates) the width of the pulses – hence Pulse Width Modulation.
Can I use a potentiometer to control motor speed?
You CAN vary the speed with a simple potentiometer. BUT you must use a pot of a resistance value appropriate for the circuit. In your example you use a power source with a low impedance, and your motor has a low impedance.
Can I control the speed of a DC motor with Arduino?
IN1 pin of the L298 IC is connected to pin 8 of the Arduino while IN2 is connected to pin 9. These two digital pins of Arduino control the direction of the motor. The EN A pin of IC is connected to the PWM pin 2 of Arduino. This will control the speed of the motor.
How do you slow down DC motor speed?
Most DC motors can be slowed down by reducing the supply level of power, Volts, lower volts and resulting less amps, will create less electrical field and will slow motor down. For more gradual speed control there are electronic solutions that are called PWM (Pulse Width Modulation) controllers or Mosfet H bridges.
How do you control speed and torque of a DC motor?
To control DC motors torque, a DC drive will regulate armature current. The armature voltage is unregulated allowing the motor to operate at whatever speed is necessary to achieve the set current /torque level.
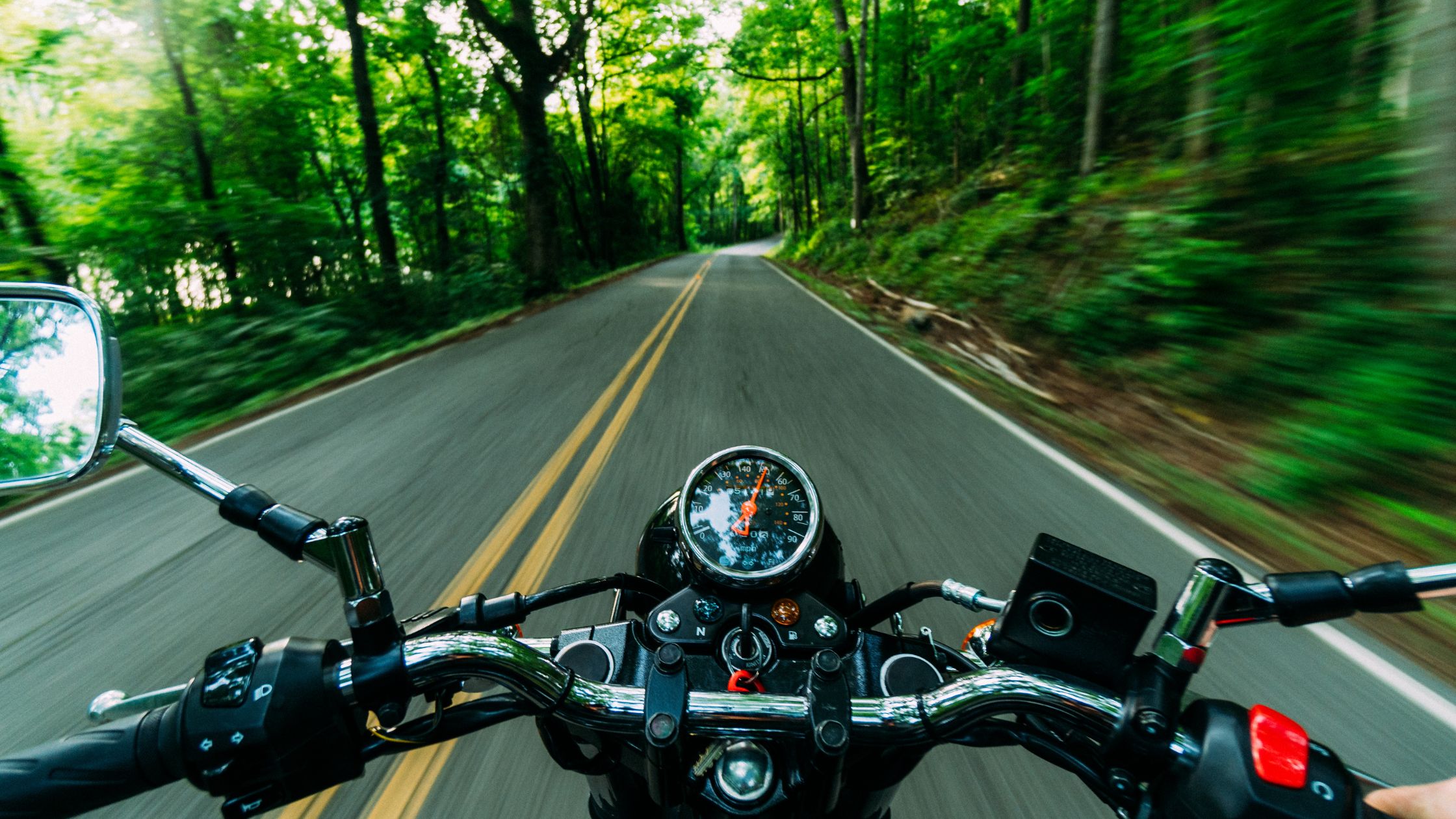
What happens if PWM frequency is too high?
Too much higher and you will be heating up your switches. You may also want to go towards the higher end to get out of the audible range.
Can you PWM A brushless motor?
PWM has many advantages and is the most widely used solution for brushless DC drivers. Setting an adequate PWM voltage and using a high PWM frequency will help to reduce the ripple and can avoid the use of additional inductances.
How fast does PWM need to be?
Typically at least 50 kHz is recommended for maxon motors. All maxon’s ESCON and EPOS4 product types have a PWM frequency in between 50 … 100 kHz.
Why PPM is better than PWM?
In PWM width of the pulses shows proportionality with the amplitude of the message signal. Whereas in PPM the position of the pulses is proportional to the amplitude of analog modulating signal. PAM technique shows low immunity towards the noise.
Why PWM is used in inverter?
Advantages of using PWM (Pulse Width Modulation) Inverter Use of PWM Techniques reduces the harmonic content in the output (load) AC voltage. PWM inverter have less harmonic content compared to square wave inverter for same fundamental voltage.
How do microcontrollers generate PWM?
Most microcontrollers have a built-in timer that can be used to generate a PWM signal. PWM outputs can be converted to a dc voltage by using a series of RC low pass filters to average the pulses. Thus, a filtered PWM circuit is a simple low cost method to convert digital to analog (i.e. create a DAC).
What voltage is PWM?
Pulse-width modulation (PWM) allows the BASIC Stamp (a purely digital device) to generate an analog voltage. The basic idea is this: If you make a pin output high, the voltage at that pin will be close to 5 V. Output low is close to 0 V.
How does PWM affect RPM?
The PWM duty cycle is used to vary the speed of the motor by controlling the motor terminal voltage. The motor voltage and revolutions per minutes (RPM) obtained at different duty cycle rates. As the duty cycle increases, more voltage is applied to the motor.
How do you choose PWM frequency?
As a rule of thumb, you want the frequency of your PWM signal to be greater than 5 over 2 pi tau, where tau is the electrical time constant for your desired motor. If you go to high, however, the transistors inside of your driver may experience thermal limitations due to switching losses.
Does PWM reduce torque?
Some of them say that the PWM reduces the average voltage (due to duty cycle) and thus, the current is also reduced and accordingly the torque is reduced too.
How do you slow down a 12 volt DC motor?
If you want to reduce rpm without compromising speed regulation then use a voltage regulator or PWM controller to lower the motor voltage. If you also want higher torque then use a gearbox (which increases torque by the same proportion as it reduces shaft rpm).
Can you put a variable speed control on any motor?
Variable frequency drives also control the speed of a motor, but they do so by changing the voltage and frequency and can thus only be used with AC motors.
Terimakasih telah membaca How To Make Pwm Dc Motor Speed Controller, semoga jawaban dari pertanyaan anda telah saya jawab semua. Semoga bermanfaat!