Jika anda sedang mencari How To Make A Motor Driver, anda berada di tempat yang tepat! Disini saya akan mencoba membahas beberapa pertanyaan mengenai How To Make A Motor Driver.
How can I make motor driver at home?
Step 1: Gather the Parts. An Arduino. A breadboard. Step 2: Wiring. Hookup all the components according to the circuit diagram shown above. Step 3: The Code. Upload the following code to arduino. Step 4: Done. Now Power the arduino and see your motor spinning with varying speeds. 37 Comments. BambiB.
What does a motor driver consist of?
Motor drivers are made from discrete components which are integrated inside an IC. The input to the motor driver IC or motor driver circuit is a low current signal. The function of the circuit is to convert the low current signal to a high current signal. This high current signal is then given to the motor.
How do DC motor drivers work?
Motor drivers acts as an interface between the motors and the control circuits. Motor require high amount of current whereas the controller circuit works on low current signals. So the function of motor drivers is to take a low-current control signal and then turn it into a higher-current signal that can drive a motor.
How do you control DC motor speed?
By varying the flux, and by varying the current through field winding. By varying the armature voltage, and the armature resistance. Through the supply voltage.
What is the price of motor driver?
L298 Motor Driver Board, Type: H-Bridge, Rs 149/piece Delta Electronic Parts | ID: 20968423991.
Do you need a motor driver?
The engine will use up a higher current level than the microcontroller. You require a motor driver module when connecting two devices that operate under different current levels to a power supply voltage. In this case, a motor acts as a third device that steps up or steps down the voltage supply.
How many types of motor drivers are there?
Types of drives There are three general categories of electric drives: DC motor drives, eddy current drives and AC motor drives.
What is a DC motor driver?
DC motor drives are defined as amplifiers or power modules that interface between a controller and a DC motor. They convert step and direction input from the controller to currents and voltages compatible with the motor.
What is a motor driver module?
It is a high voltage , high current dual full-bridge driver de-signed to accept standard TTL logic level sand drive inductive loads such as relays, solenoids, DC and stepping motors. Two enable inputs are provided to enable or disable the device independently of the in-put signals .
How does AC motor control speed?
The power applied to the motor is controlled by varying the width of these applied pulses, which in turn varies the average voltage applied to the terminals of the motor. By modulating or changing the timing of these pulses, the speed of the motor can be controlled.
What is rpm of DC motor?
DC controls adjust speed by varying the voltage sent to the motor (this differs from AC motor controls which adjust the line frequency to the motor). Typical no load or synchronous speeds for an AC fractional horsepower motor are 1800 or 3600 rpm, and 1000-5000 rpm for DC fractional hp motors.
What is H-bridge made of?
A solid-state H-bridge is typically constructed using opposite polarity devices, such as PNP bipolar junction transistors (BJT) or P-channel MOSFETs connected to the high voltage bus and NPN BJTs or N-channel MOSFETs connected to the low voltage bus.
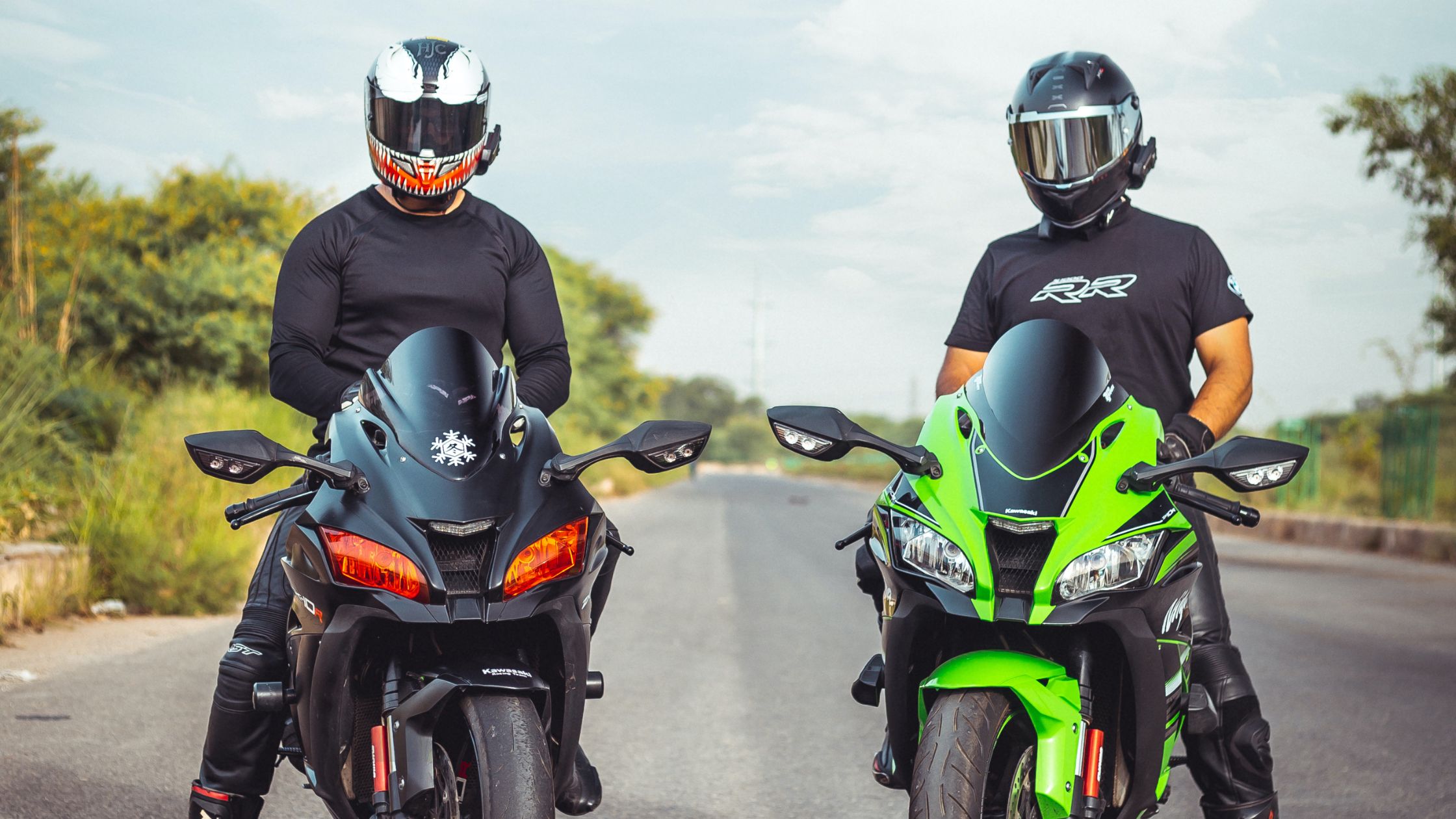
How do you control the torque of a DC motor?
To control DC motors torque, a DC drive will regulate armature current. The armature voltage is unregulated allowing the motor to operate at whatever speed is necessary to achieve the set current /torque level.
How can I run a stepper motor without Arduino?
Step 1: Get All the Stuff. Step 2: Start by Plugging on the A4988 Motor Driver on the Breadboard. Step 3: Get Help From the Circuit Schematic. Step 4: Wire Up and Test the Speed Controller. Step 5: Wire Up and Test the Direction Controller. Step 6: It’s DONE.
What controls the speed of a motor?
The rotating speed of an electric motor depends on two factors: its physical construction, and the frequency (Hz) of the voltage supply. Electrical engineers select the speed of a motor based on the needs of each application, similar to how the mechanical load determines the horsepower required.
What is the difference between a motor controller and a motor driver?
The main difference between a motor controller and a motor driver is, the motor controller is responsible for the controlling speed, torque, the direction of the motor whereas a motor driver is responsible to provide enough electrical power to the motor as per requirement.
Is motor driver and motor controller same?
‘ The TLDR is that a motor driver simply handles the power to drive the motors, whereas the logic and digital control has to be done by an external microcontroller or microprocessor, whereas a motor controller has all of the logic circuitry built in and can be controlled by a higher-level interface such as a PWM signal …
Do you need a driver for a DC motor?
So mainly, any motor usually needs a driver circuit because its voltage/current requirements are different from the device that’s trying to control it. Show activity on this post. At a high level, a motor driver takes a “logic-level” input (desired “effort”) and delivers a corresponding “high-side” output to the motor.
What is AC motor drives?
An AC drive is a device used to control the speed of an electrical motor in order to: enhance process control. reduce energy usage and generate energy efficiently. decrease mechanical stress on motor control applications.
Can a DC motor turn both ways?
DC motors, like AC motors, can be configured to turn in either direction. Their direction can be easily controlled by inverting the polarity of the applied armature voltage by reversing the armature leads. This works with shunt, series, and compound wound DC motors.
How does Raspberry Pi control motor speed?
By pressing one button the, speed of DC motor increases and by pressing the other button, the speed of DC motor decreases. With this we have achieved the DC Motor Speed Control by Raspberry Pi.
What can I use instead of potentiometer?
Magnetic encoder modules offer non-contact alternative to potentiometers. Potentiometers provide low cost, analogue position feedback with simple integration. However, they are subject to degradation of performance, or even failure, due to wear and contamination.
Can any motor be variable speed?
A: In general if you don’t do anything special to it, a DC motor will have variable speed. The main factors are the DC voltage applied to the armature coil and the amount of torque load you are trying to drive. In order to make it into a constant speed DC motor you have to have some sort of electronic feedback.
How many volts can a DC motor take?
Typical DC motors may operate on as few as 1.5 Volts or up to 100 Volts or more. Roboticists often use motors that operate on 6, 12, or 24 volts because most robots are battery powered, and batteries are typically available with these values. Operating Current.
Terimakasih telah membaca How To Make A Motor Driver, semoga jawaban dari pertanyaan anda telah saya jawab semua. Semoga bermanfaat!