Jika anda sedang mencari How To Drive Servo Motor With Plc, anda berada di tempat yang tepat! Disini saya akan mencoba membahas beberapa pertanyaan mengenai How To Drive Servo Motor With Plc.
Do I need a motor driver for a servo motor?
You don’t need this shield to drive servo motors, they have their own controller, you need just a 5V power line, GND and digital output pin to generate a PWM and that’s it.
What is the difference between servo drive and servo motor?
What Is a Servomotor and What Is a Servo Drive? A servomotor is a structural unit of a servo system and is used with a servo drive. The servomotor includes the motor that drives the load and a position detection component, such as an encoder.
Can a PLC drive a stepper motor?
Wiring PLC to Stepper Motor You will need a Stepper Driver to interface between the PLC’s step and direction signals and the Stepper Motor. Often the inputs to Stepper Drivers include differential pairs for Step and Direction, consisting of Step+, Step-, Dir+ and Dir-.
Can a PLC run a stepper motor?
In this application PLC is used to control the operation of a stepper motor. Ladder Logic Diagram, the PLC program, uses step ladder instructions for implementation of the control algorithm. The motion control algorithm includes the control of stepper motor speed and direction of rotation.
What is the use of encoder in servo motor?
The servo motor consists of a brushless DC or AC motor, an encoder, and a servo amplifier (also called a driver). In order to keep the rotation speed of a brushless DC motor or AC motor constant, an encoder detects the rotation speed.
Which is better DC or servo motor?
Pros: The position of servo motors can be controlled more precisely than those of standard DC motors, and they usually have three wires (power, ground & control) As the servo motors are designed for precise angular movement, they are more suitable for the applications where the angular movement should be accurate.
How do I choose a servo driver?
Motor types commonly paired with servo drives. Commutation prompted by the servo drive. Feedback. Voltage and current. Operating mode. Analog or digital. Communication. Integrated safety.
Why do we need a servo driver?
In essence, the role of the servo drive is to translate low power command signals from the controller into high power voltage and current to the motor. Depending on the application, the servo drive can regulate and properly coordinate the motor’s desired position, speed, torque, etc.
Is a servo drive an inverter?
The inverter is usually composed of four parts: rectifier unit, high-capacity capacitor, inverter and controller. The servo system is an automatic control system that enables the output controlled quantity of the object’s position, orientation, state, etc. to follow any change of the input target (or a given value).
Does servo use PPM or PWM?
Servos does not use PWM, it uses PPM: PWM = Pulse width modulation, The pulse start at 0ms, and is high for the percentage of the time compared to the percentage of the voltage you want, 5v signal, if you want 1v, the pulse is 20ms High and 80ms Low.
Can we control servo motor speed?
By using map() and millis() functions, we can control the speed of servo motor smoothly without blocking other code. The below example shows how to move the servo motor from 30° to 90° in 3 seconds.
How fast can a servo motor spin?
In a normal position servo, 1mS will make it move from wherever it was to one end of its travel, at the fastest the servo can manage. 2mS will make it move to the other end. If you step between 1 and 2mS length pulses, then it will do this as fast as it can.
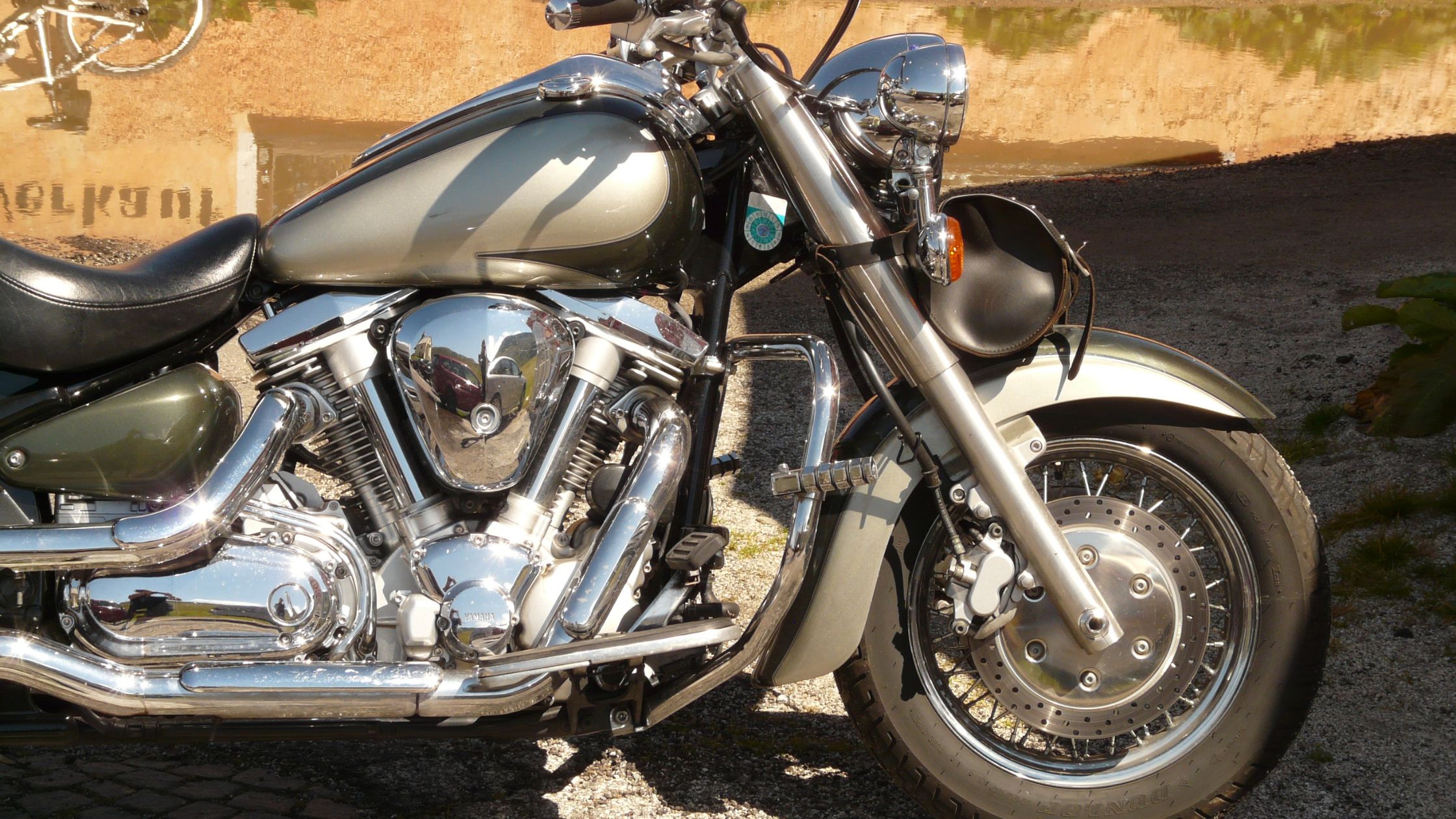
What is the difference between variable speed drive and variable frequency drive?
A variable frequency drive (VFD) refers to AC drives only and a variable speed drive (VSD) refers to either AC Drives or DC Drives. VFDs vary the speed of an AC motor by varying the frequency to the motor. VSDs referring to DC motors vary the speed by varying the voltage to the motor.
How do CNC servo motors work?
Servo motors use closed-loop circuitry to transfer information to the CNC machine. A regular DC or AC motor is connected to an encoder fixed with a sensor. Servo motors have high accuracy and resolution owing to the sensor-fixed encoder. The motor is powered by the servo amp, which also counts the steps made.
Is a servo motor A DC motor?
Servo motors are generally an assembly of four things: a DC motor, a gearing set, a control circuit and a position-sensor (usually a potentiometer). The position of servo motors can be controlled more precisely than those of standard DC motors, and they usually have three wires (power, ground & control).
What are the three types of servomotor?
Servo motors come in many sizes and in three basic types. The three types include positional rotation, continuous rotation, and linear.
Do servo motors need VFD?
Key Differences Between VFD and Servo Drives While Servo Drives can’t work without an encoder for electronic commutation, a VFD can work perfectly fine without it. The Servo Drive is used for controlling permanent magnet motors, whereas VFDs are used for control of a squirrel-cage type motor.
Can you run a servo motor with a VFD?
Using variable frequency drives for the servo motor is quite possible, only if the application is not critical in positioning control purpose.
Do servos need a PWM pin?
You can connect a servo to any digital pin. You can have PWM on any pin.
What is the input signal to a servo motor?
Answer. (a) digital signal.
How much weight can a servo lift?
Also operating at 4.8V, this servo motor can drive a load up to 3.3kg/cm (Stall Torque). At 6V, the high end of the test voltage, the servo can move 60° at a speed of . 16 seconds with no load, and has a higher torque limit of 4.1kg/cm.
How do you make a motor stay in position?
In order to hold it in place, the driver has to keep pressing the button over and over again. Any help would be appreciated. First of all, I would suggest adding rubber bands to your lift. The rubber bands often can add enough tension which will allow your lift to remain up even when no motor power is being applied.
Why do we put a drive between the microcontroller and stepper motor?
Stepper Motor Control using 8051 Microcontroller Principle The main principle of these circuits is to rotate the stepper motor step wise at a particular step angle. The ULN2003 IC and the L293D Motor Driver are used to drive the stepper motor as the controller cannot provide current required by the motor.
What is the difference between servo motor and stepper motor?
Stepper motors have a high pole count, usually between 50 and 100. Servo motors have a low pole count – between 4 and 12. This difference in pole count means that stepper motors move incrementally with a consistent pulse in a closed loop system. Servo motors require an encoder to adjust pulses for position control.
Terimakasih telah membaca How To Drive Servo Motor With Plc, semoga jawaban dari pertanyaan anda telah saya jawab semua. Semoga bermanfaat!