Jika anda sedang mencari How To Control Motor Dc Speed Using Pid, anda berada di tempat yang tepat! Disini saya akan mencoba membahas beberapa pertanyaan mengenai How To Control Motor Dc Speed Using Pid.
How can PID be used to control DC motor speed?
The Discrete PID controller is used to measure the Speed, Torque and Voltage of the DC motor and then send it back as feedback. The implementation of the speed block is shown in figure 5. Using this feedback the difference between the set speed and actual speed is slowly removed.
What is PID in DC motor?
The proportional-integral-derivative (PID) controller is a control loop feedback mechanism widely used in industrial control systems. A PID controller calculates an error value as the difference between the desired set point and a measured process variable.
What is PID speed control?
A proportional–integral–derivative controller (PID controller or three-term controller) is a control loop mechanism employing feedback that is widely used in industrial control systems and a variety of other applications requiring continuously modulated control. A PID controller continuously calculates an error value.
How does a PID controller work?
PID Controller Working Principle The working principle behind a PID controller is that the proportional, integral and derivative terms must be individually adjusted or “tuned.” Based on the difference between these values a correction factor is calculated and applied to the input.
How do you tune a PID?
Manual PID tuning is done by setting the reset time to its maximum value and the rate to zero and increasing the gain until the loop oscillates at a constant amplitude. (When the response to an error correction occurs quickly a larger gain can be used. If response is slow a relatively small gain is desirable).
What is the transfer function of PID controller?
The transfer function of a PID controller is found by taking the Laplace transform of Equation (1). = derivative gain. C = s^2 + s + 1 ———– s Continuous-time transfer function. C = 1 Kp + Ki * — + Kd * s s with Kp = 1, Ki = 1, Kd = 1 Continuous-time PID controller in parallel form.
What is PID encoder?
In industrial automation and control, PID controller has become one of the most reliable control algorithms that can be implemented to stabilize the output response of any system. PID stands for Proportional-Integral-Derivative.
Why PID controller is better?
In PID controller there is a minor decrease or no changes are shown in various parameter which can see from table 1 and table 2. Hence there is no change in steady state error so PID controller is better than P and PID controller.
What is the advantage of PID controller?
The advantage of PID controller is its feasibility and easy to be implemented. The PID gains can be designed based upon the system parameters if they can be achieved or estimated precisely.
What is the output of PID controller?
Output. The PID controller output is calculated by simply adding the Proportional, the Integral and the Derivative. Depending on the gain setting of these three values, will determine how much effect they will have on the output.
How do you speed up a PID loop?
The art of tuning a PID loop is to have it adjust its output (OP) to move the process variable (PV) as quickly as possible to the set point (responsive), minimize overshoot, and then hold the variable steady at the set point without excessive OP changes (stable).
Why PID tuning is required?
The main objective in tuning PID controllers is to adjust the reactions of PID controllers to setpoint changes and unmeasured disturbances such that variability of control error is minimized. PID controllers are implemented primarily for the purpose of holding measured process value at a setpoint, or desired value.
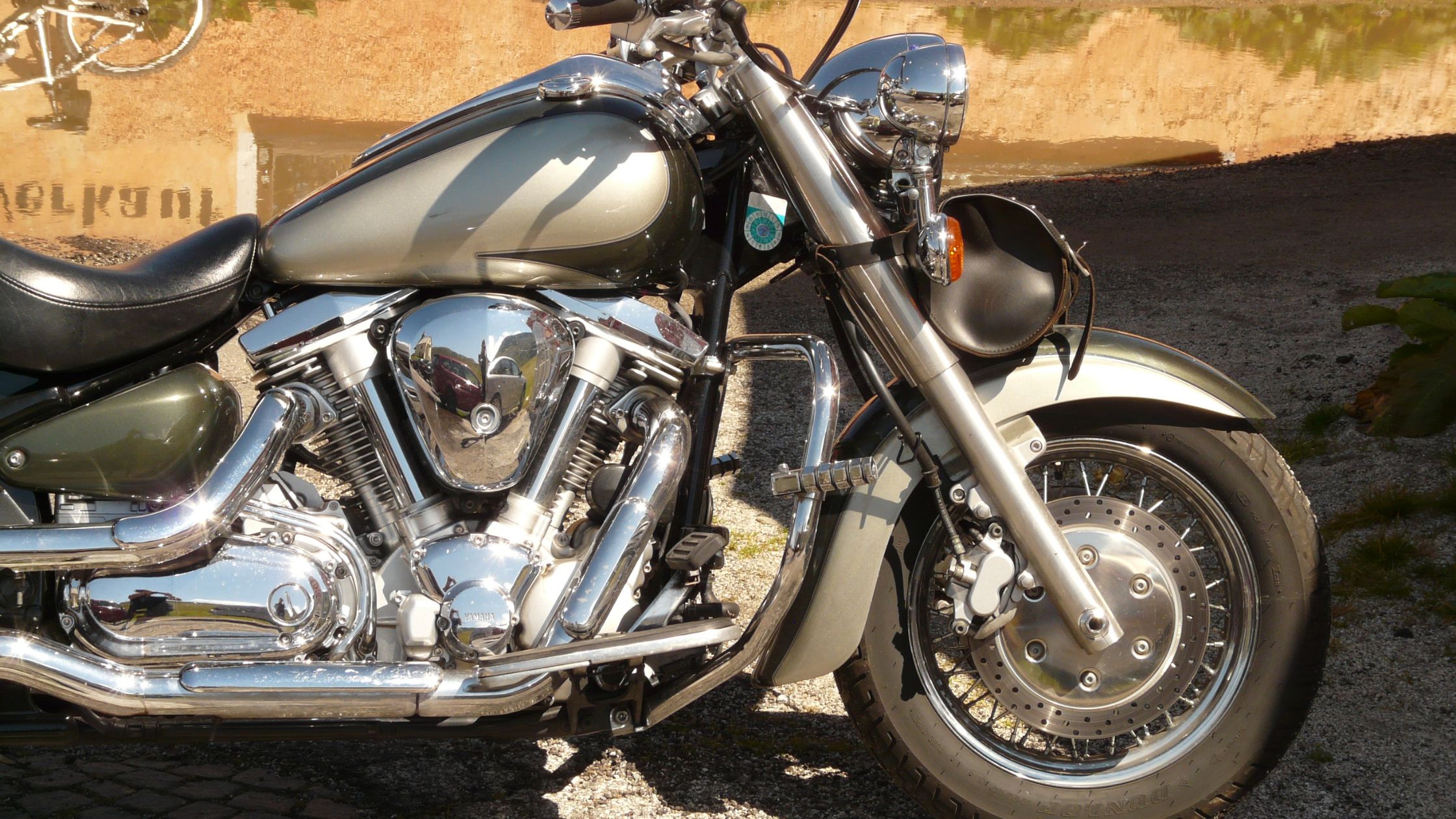
Where are PID controllers used?
Proportional-Integral-Derivative (PID) controllers are used in most automatic process control applications in industry today to regulate flow, temperature, pressure, level, and many other industrial process variables.
Is Arduino a PID controller?
The second part deals with the designing of our system, an Arduino-based temperature controller system using the PID algorithm. The codes written in C programming serve as the software portion, while the hardware portion includes Arduino UNO, electronic components, and solid state devices.
What is feed forward in PID?
Feed forward augmentation is a prediction technique that estimates the output from a proportional-integral-derivative (PID) control algorithm without waiting for the PID algorithm to respond. Feed forward reduces the error faster or keeps the error smaller than relying on the PID algorithm alone.
What is a PID FRC?
The PID controller is a commonly used feedback controller consisting of proportional, integral, and derivative terms, hence the name.
How does a VFD control motor speed?
A variable frequency drive controls the speed of an AC motor by varying the frequency supplied to the motor.
How does DC motor controller work?
A DC motor controller manipulates the position, speed, or torque of a DC-powered motor and easily reverses, so the DC motor drive current runs in the opposite direction. Enjoy higher starting torque, quick starting and stopping, reversing, variable speeds with voltage input and more.
How does a motor speed controller work?
How does a motor speed controller work? All 4QD controllers work by switching the battery connection to the motor on and off around 20,000 times a second using a technique called pulse width modulation [PWM].
How do you increase motor speed?
Magnetic flux – By decreasing the flux, the speed of the motor can be increased. The flux can be changed by changing the current with a shunt field rheostat. Resistance of the armature circuit – By decreasing the resistance, there is increase in the armature current which causes a larger torque to be developed.
How can a DC motor have more torque?
To increase the torque (if 9V won’t get it high enough) you can increase the supply voltage, and to decrease the speed you can pulse width modulate (PWM) the supply input to the motor.
Why PID controller is not used?
Because of the use of derivative control, PID control cannot be used in processes where there is a lot of noise, since the noise would interfere with the predictive, feedforward aspect. However, PID control is used when the process requires no offset and a fast response time.
Which is better PI or PD?
In terms of speed, PID controller has the fastest response as it shows the fastest time constant of 0.17s and settling time compared to the PD and PI Controllers, however in terms of Damping the PD controller has the best performance because no overshoot was observed at steady state compared to the PI and PID …
What is the difference between PD and PID controller?
A PD controller reduces the transients like rise time, overshoot, and oscillations in the output. Useful for changing magnitude and want to add phase lead to the output. A PID controller is a general form of controller. The gains of the three control actions can be adjusted to achieve any controller.
Terimakasih telah membaca How To Control Motor Dc Speed Using Pid, semoga jawaban dari pertanyaan anda telah saya jawab semua. Semoga bermanfaat!