Jika anda sedang mencari How To Connect Stepper Motor To Tb6560, anda berada di tempat yang tepat! Disini saya akan mencoba membahas beberapa pertanyaan mengenai How To Connect Stepper Motor To Tb6560.
Can you connect a stepper motor directly to an Arduino?
Generally, stepper motors cannot be controlled by an Arduino pin. They have a current draw of over the 20mA any single pin can supply. Kickback is also a problem. Because the motors have moving magnetic parts inside, they will continue to generate electricity after power has been cut.
Can I run a stepper motor from a PLC?
Wiring PLC to Stepper Motor You will need a Stepper Driver to interface between the PLC’s step and direction signals and the Stepper Motor. Often the inputs to Stepper Drivers include differential pairs for Step and Direction, consisting of Step+, Step-, Dir+ and Dir-.
How can a PLC control a motor?
A PLC has to start a Motor when the Start button is pressed. It has three interlocks which are Motor Vibration High, Overload & Motor Temperature High. if any of the interlock activated then PLC has to stop the motor immediately. PLC has to stop the motor if the stop button is pressed.
How is a stepper motor controlled?
They use open-loop control, and are operated by having a controller generate pulses that are input to a driver, which in turn supplies the drive current to the motor. Stepper motors are controlled by input of electrical pulses, such that the speed of motor rotation is proportional to the input pulse rate.
Where are stepper motors connected?
Connecting a bipolar stepper motor with four or six leads These two-phase stepper motors have one coil per phase, with one lead connected to each end of each coil. Versions with six leads also provide access to the centers of the two coils so that the motor can optionally be controlled by a unipolar driver.
How do you start and stop a stepper motor?
Rotate wheel 30 degrees and stop. Turn on Solid State Relay ,which is attached to a small pump, the pump stays on for 2 seconds adds some water. Wait 5 seconds for drips to stop. Rotate to next position and repeat above. Do this for all 12 positions.
How do you interface a stepper motor to a controller give the necessary hardware and software functional blocks?
Initialize the port pins used for the motor as outputs. Write a common delay program of say 500 ms. Output first sequence-0 × 09 on the pins. Call delay function. Output second sequence-0 × 0 c on the pins. Call delay function. Output third sequence-0 × 06 on the pins. Call delay function.
What is a stepper motor driver board?
The Quadstepper motor driver board allows you to control up to 4 bipolar stepper motors simultaneously using logic level IO pins. Each motor driver has an output drive capacity of 35V and 1Amps. The board is capable of driving motors in full, half, quarter, eight, and sixteenth-step modes.
Can a PLC control a 3 phase motor?
Using the PLC So a PLC can also be used to control the operation of a VFD, hence to finally control the connected 3 Phase Induction Motor.
How does PLC control motor speed?
The PLC has to give set point for VFD drive to control the motor speed, this can achieved either automatically from the PLC or by the operator action from the HMI. According to set point value, PLC will control the drive speed and VFD drive finally controls the motor speed.
Do you need an encoder with a stepper motor?
While having full control of rotation and speed, the simple structure of stepper motors is achieved without using electrical components, such as an encoder within the motor.
Can stepper motors turn both ways?
yes, stepper motors can move in both directions.
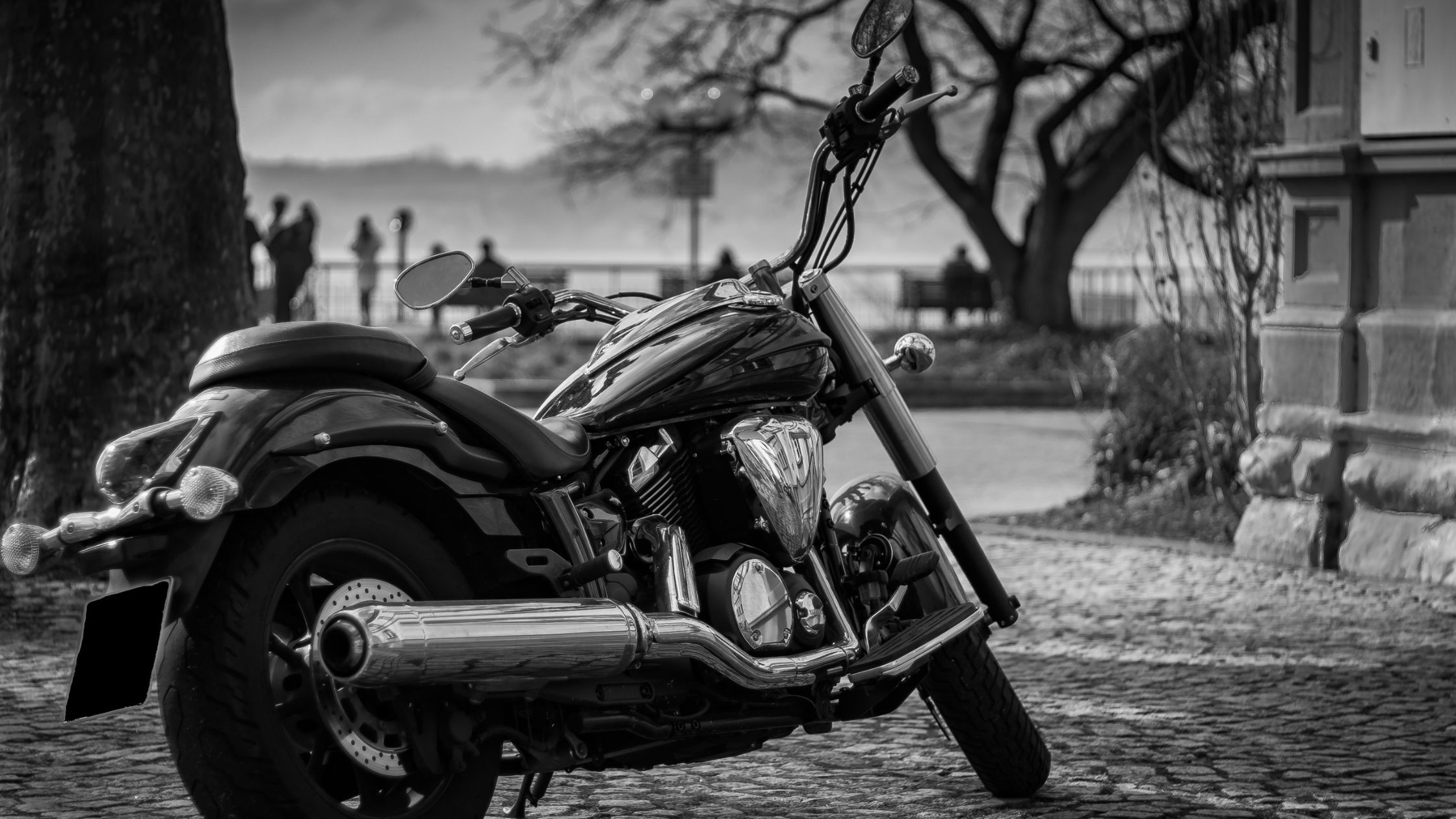
What is the maximum rpm of a stepper motor?
If you want to know about stepper motor max speed, you should know that the maximum speed that’s typical of a stepper motor is 1000rpms while the max speed of gearmotors comes in at 400-550 RPM. That said, the speed of any stepper motor depends on the specifications of the controller that comes with it.
How do you stop a stepper motor?
Call stepper. stop() function: This way does NOT stop the stepper motor immediately but gradually. Do NOT call stepper. run() function: This way stops the stepper motor immediately.
Can an Arduino Nano run a stepper motor?
Introduction: Arduino Nano and Visuino: Control Stepper Motor With Buttons. Stepper motors are often used in Arduino projects, whenever something needs to be moved or turned. In this Instructable, I will show you how easy it is to connect Stepper Motor to Arduino Nano and control it with Buttons.
How many pins does stepper motor have?
The following 4 pins are for connecting the motor. The 1A and 1B pins will be connected to one coil of the motor and the 2A and 2B pins to the other coil of the motor.
What happens when you overload a stepper motor?
When a stepper motor gets overloaded, mechanicly, is stops, it “stalls” and the rest of the movement is lost.
How do you interface a stepper motor to a controller?
Interfacing Stepper Motor with 8051 Microcontroller Weare using Port P0 of 8051 for connecting the stepper motor. HereULN2003 is used. This is basically a high voltage, high current Darlington transistor array. Each ULN2003 has seven NPN Darlington pairs.
Which port is used in stepper motor?
Featured in this project is the control of a stepper motor with its speed, direction, and step size by sending some signals through the parallel port.
Why do we put a driver between the microcontroller and the stepper motor?
Stepper Motor Control using 8051 Microcontroller Principle The main principle of these circuits is to rotate the stepper motor step wise at a particular step angle. The ULN2003 IC and the L293D Motor Driver are used to drive the stepper motor as the controller cannot provide current required by the motor.
Can you control a motor with a PLC?
PLC and motor control application This motor control application can also be accomplished with a PLC. In the following example, a normally open Start pushbutton is wired to the first input (I0. 0), a normally closed Stop pushbutton is wired to the second input (I0.
Can a VFD be used on any 3 phase motor?
Yes, a VFD can power a three-phase motor with a single-phase input power supply, but phase conversion introduces many considerations that normally don’t factor in to buying a VFD.
How does a VFD connect to a motor?
Connect the cable shield to PE potential properly, i.e. with good conductivity, on both sides. The motor cables must be kept physically separate from the control and network cables.
What are the 5 PLC programming languages?
Ladder Diagram (LD). Sequential Function Charts (SFC). Function Block Diagram (FBD). Structured Text (ST). Instruction List (IL).
Terimakasih telah membaca How To Connect Stepper Motor To Tb6560, semoga jawaban dari pertanyaan anda telah saya jawab semua. Semoga bermanfaat!