Jika anda sedang mencari Do Dcc Motor Need Pwn Pin, anda berada di tempat yang tepat! Disini saya akan mencoba membahas beberapa pertanyaan mengenai Do Dcc Motor Need Pwn Pin.
Do DC motors use PWM?
PWM (Pulse Width Modulation) One method that is often used for DC motor control using a microcontroller is Pulse Width Modulation (PWM) method. The speed of the electric motor depends on the modulator voltage. The greater the voltage, the faster the rotation of an electric motor.
Why PWM is used in DC motor?
Pulse width modulation is a great method of controlling the amount of power delivered to a load without dissipating any wasted power. The above circuit can also be used to control the speed of a fan or to dim the brightness of DC lamps or LED’s. If you need to control it, then use Pulse Width Modulation to do it.
What is best PWM frequency for DC motor?
Choose the frequency that provides the best balance of torque throughout the desired speed range while balancing the motor chatter that can happen at lower frequencies. As a rule of thumb, most small brushed DC motors will operate nicely with a PWM frequency of 50Hz to 100Hz and slow decay mode.
Is PWM AC or DC?
Any other voltage or current that changes over time can be called AC so a PWM signal is AC as long as it isn’t a 0 % (exactly) or 100% (exactly) PWM signal because those signals are constant and thus they’re DC.
How do you control the speed of a DC motor?
By varying the flux, and by varying the current through field winding. By varying the armature voltage, and the armature resistance. Through the supply voltage.
How does PWM affect RPM?
The PWM duty cycle is used to vary the speed of the motor by controlling the motor terminal voltage. The motor voltage and revolutions per minutes (RPM) obtained at different duty cycle rates. As the duty cycle increases, more voltage is applied to the motor.
Which mode is used for speed control of DC motor?
The speed control of DC Motor using both PI and Sliding mode controllers is studied and the results are compared. The simulation results show that Sliding mode controller is superior than PI for speed control of DC motor. Since the SMC is robust in presence of disturbances, the desired speed is perfectly tracked.
What is the disadvantage of PWM?
Disadvantage of PWM The disadvantages of PWM may be described by under: Due to the variable pulse width, the pulses have variable power contents. Hence, the transmission must be powerful enough to handle the maximum width, pulse, though the average power transmitted can be as low as 50% of this maximum power.
What is the purpose of PWM?
The pulse width modulation technique is used in telecommunication for encoding purposes. The PWM helps in voltage regulation and therefore is used to control the speed of motors. The PWM technique controls the fan inside a CPU of the computer, thereby successfully dissipating the heat.
Why do we need pulse width modulation?
The main advantage of PWM is that power loss in the switching devices is very low. When a switch is off there is practically no current, and when it is on and power is being transferred to the load, there is almost no voltage drop across the switch.
How do you control the speed of a 24V DC motor?
The easiest way to control a relatively low current 12-24V motor is by using a generic analog DC motor speed controller. This type of controller has a potentiometer to vary the speed of the motor. These controllers can be found with a wide range of power ratings.
How can we change speed of DC motor using PWM?
If such a signal is fed to a DC motor, we can change the speed of the motor by changing the duty cycle of the PWM signal. The change in pulse width is created by increasing the on-time (HIGH value) of the pulse while reducing the off-time (LOW value) by the same amount so that the frequency of the signal is constant.
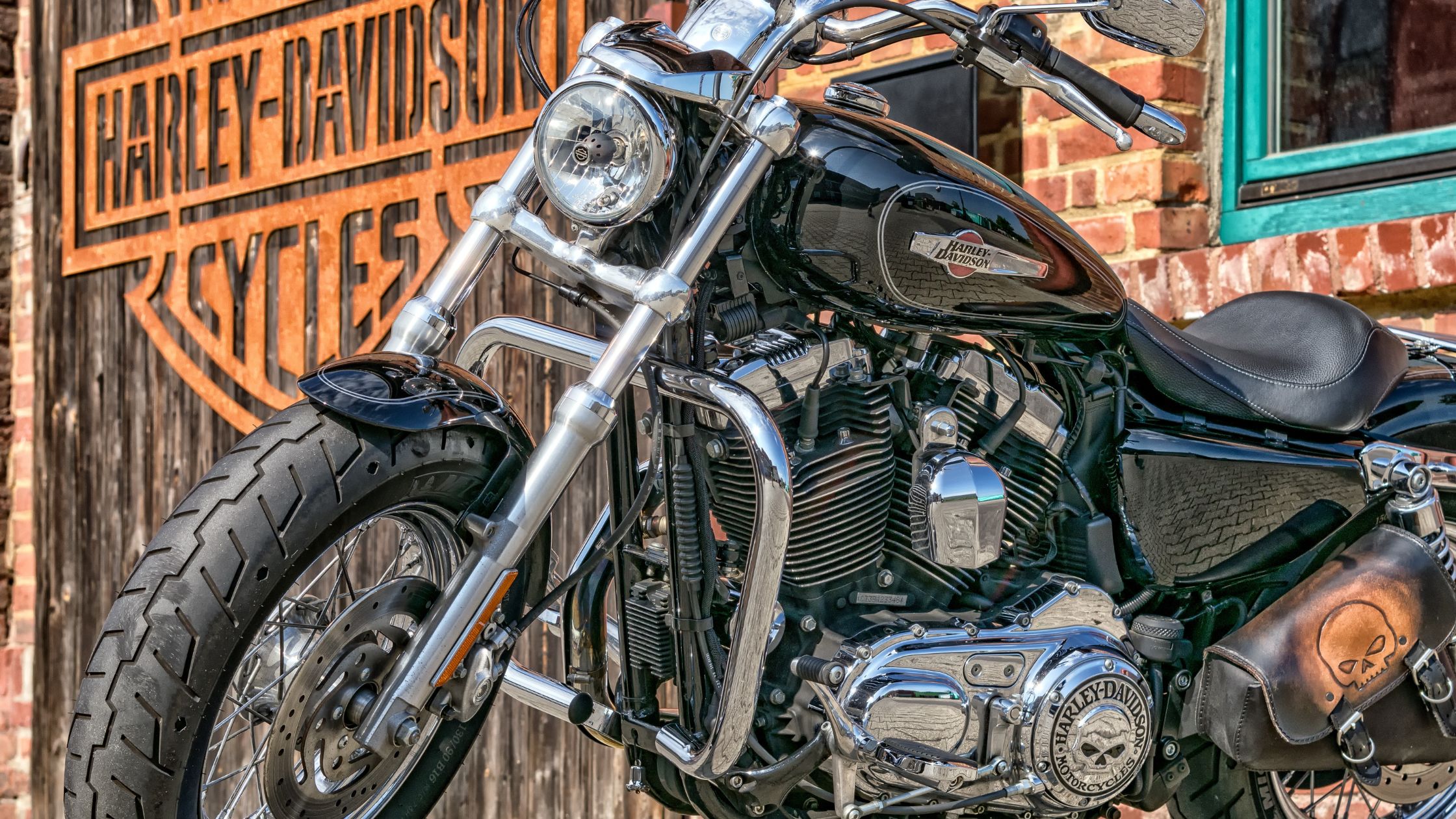
What happens if PWM frequency is too high?
Too much higher and you will be heating up your switches. You may also want to go towards the higher end to get out of the audible range.
How does PWM affect torque?
PWM regulates the torque through duty cycle and should ideally respond linearly, 50% duty cycle, 50% torque. Frequency primarily affects resolution of regulation, vibrations (change of torque on timescale of one PWM cycle) and audible noise.
Does PWM frequency Matter?
To a first approximation, frequency does not matter at all, provided it’s fast enough to avoid the appearance of blinking. All that’s important is the average power of the LED, which depends only on the duty cycle. In practice, there are switching losses that increase with frequency.
Does PWM reduce voltage?
PWM does not lower the (peak) voltage. PWM reduces the average current (and in consequence the average power). In case of LEDs – they don’t care much about the voltage, it is the current that can destroy them (both forward and reverse). So you have to take care not to exceed their peak current rating.
Does PWM work with AC?
By coupling the control of the pulse width and the pulse group period, PWM drives provide a means to control both the voltage and frequency output to an AC motor. The ability to control the torque and speed of an AC motor opens up application possibilities for machine designers.
How do you slow down a 12 volt DC motor?
Reduce the supply voltage. For a little hobby motor, use a smaller battery. For larger motors, a PWM (pulse width modulation) controller is required. These have various current ratings, and you need one that is rated at or above the maximum draw of the motor.
Does PWM change torque?
However there are many other guys who say that a PWM contoller affects only the speed of a motor ( voltage control) but the current is staying constant. Thus the PWM is NOT affecting the torque (and the current) but only the speed (and the voltage).
Do brushless motors use PWM?
PWM has many advantages and is the most widely used solution for brushless DC drivers.
Can PWM control RPM?
However, when using only one PWM fan, a designer can program a desired temperature/RPM curve by simply changing the PWM controller software.
What are 3 types of motor controls?
There are four basic motor controller and drive types: AC, DC, servo, and stepper, each having an input power type modified to the desired output function to match with an application.
What is the major drawback of armature control for controlling the speed of DC motor?
Drawbacks of armature resistance control method: It is restricted to keep the speed below the normal speed of the motor and increase in the speed above normal level is not possible. For a given value of variable resistance, the speed reduction is not constant but varies with the motor load.
How do you control a separately excited DC motor?
The speed of separately excited dc motor can be control by changing the armature voltage and changing field flux. Due to this the speed can be controlled for below rated speed and speed above the rated speed, respectively.
Terimakasih telah membaca Do Dcc Motor Need Pwn Pin, semoga jawaban dari pertanyaan anda telah saya jawab semua. Semoga bermanfaat!