Jika anda sedang mencari How To Contro Motor Stepper With Uln 2003, anda berada di tempat yang tepat! Disini saya akan mencoba membahas beberapa pertanyaan mengenai How To Contro Motor Stepper With Uln 2003.
Why do we need a ULN2003 in driving a stepper motor?
Known for its high current and high voltage capacity, the ULN2003 gives a higher current gain than a single transistor and enables the low voltage and low current output of a microcontroller to drive a higher current stepper motor.
How do I use ULN2003?
Just attach the different loads with a different power source with ULN2003. Then Connect each load with a different power source. After that Common the ground with IC. Each Input pin controls each output.
Can you control a stepper motor with a potentiometer?
In this example, a potentiometer (or other sensor) on analog input 0 is used to control the rotational speed of a stepper motor using the Arduino Stepper Library. The stepper is controlled by with digital pins 8, 9, 10, and 11 for either unipolar or bipolar motors.
How does a stepper motor be interfaced with microcontroller?
An external crystal oscillator is connected to the 18 and 19 pins of the microcontroller. The motor is connected to the port2 of the microcontroller through a driver IC. The ULN2003A is a current driver IC. It is used to drive the current of the stepper motor as it requires more than 60mA of current.
What is the difference between ULN2003 and ULN2004?
The main difference between the ULN2003 and the ULN2004 is the value of the resistor between input and base of the darlington transistor.
Can you control stepper motor speed?
The angle and speed of rotation of stepper motors can be controlled simply and accurately by means of input pulses. This capability is put to use in a wide range of equipment and electronic devices.
Can you run a stepper motor without a computer?
This instructable will show you how to control stepper motors (Unipolar OR Bipolar) manually with a knob, without the use of a PIC or PC, so no programming is needed. The position of the knob determines the position of the motor shaft, which will stay in that position until the knob is turned again.
Can potentiometers be variable resistor?
The potentiometer is the most common variable resistor. It functions as a resistive divider and is typically used to generate a voltage signal depending on the position of the potentiometer.
How is pulse generated from microcontroller for stepper motor control?
The programmed microcontroller generates stepped electrical pulses at regular intervals to the stepper motor for rotating the solar panel. The driver IC is used to drive the stepper motor as the controller is unable to provide the power requirements of the motor.
What is the main idea of PWM in motor control using microcontroller?
Armature voltage is varied by pulse width modulation (PWM) of input DC voltage by using the developed microcontroller’s program. Thus the speed of the DC motor is changed. Direction of rotation of DC motor is changed by initiating an interrupt signal to the microcontroller using push switches.
What is uln2003apg?
The ULN2003A is an array of seven NPN Darlington transistors capable of 500 mA, 50 V output. It features common-cathode flyback diodes for switching inductive loads. It can come in PDIP, SOIC, SOP or TSSOP packaging.
What is IC ULN2004?
The UTC ULN2004 are high-voltage, high-current darlington drivers comprised of seven NPN darlington pairs. All units feature integral clamp diodes for switching inductive loads. Applications include relay, hammer, lamp and display (LED) drivers.
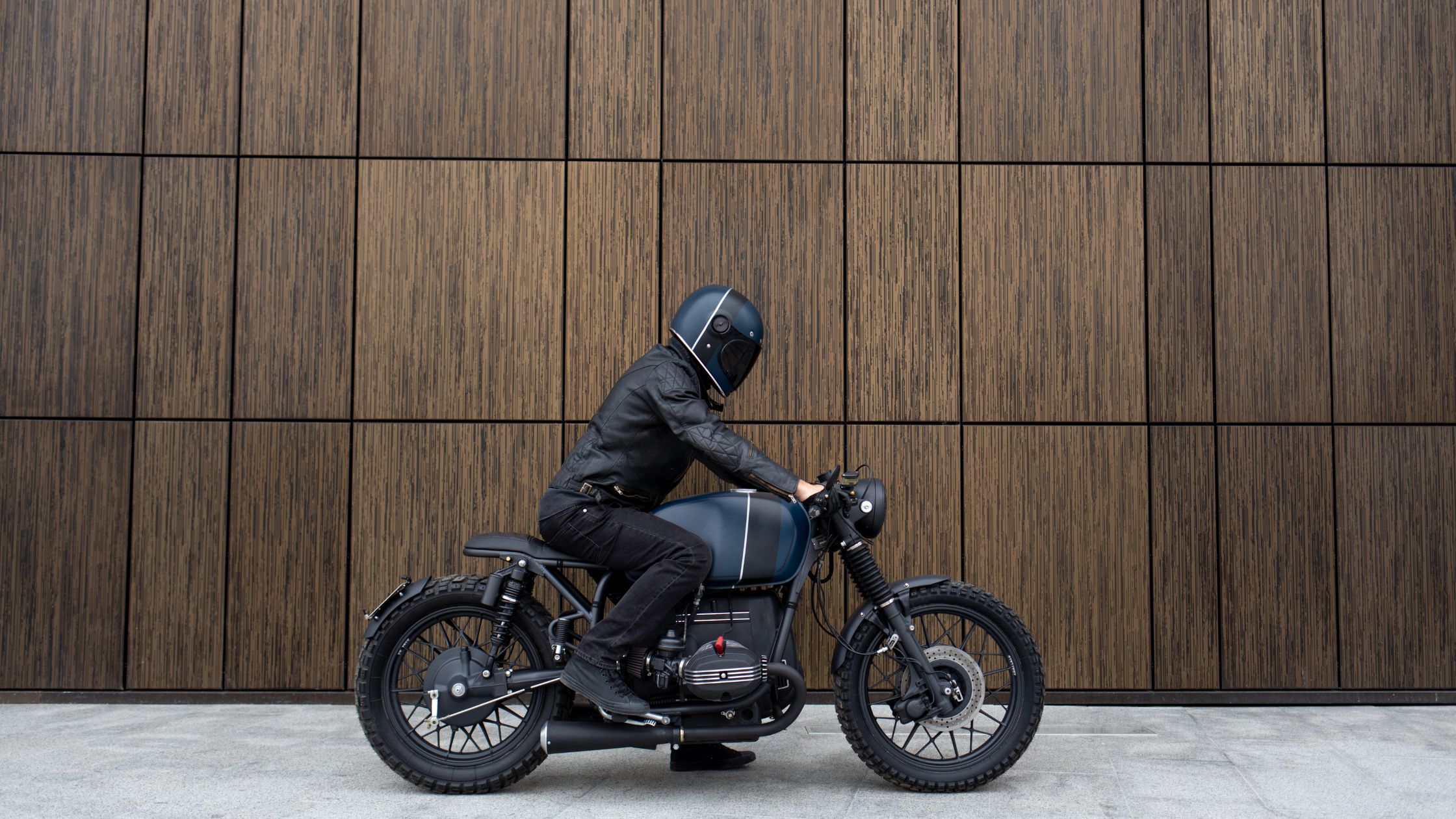
How do I change the RPM on my stepper motor?
There are two ways you can control the speed of your stepper motor. You can either decrease the delay time between each step or you can adjust the size of the step the motor takes. Decreasing the delay time is straightforward, just lower the delayMicroseconds and the stepper motor will have an increased step rate.
How do you change the speed and direction of a stepper motor?
Step 1: Get All the Stuff! Step 2: Start by Plugging on the A4988 Motor Driver on the Breadboard. Step 3: Get Help From the Circuit Schematic. Step 4: Wire Up and Test the Speed Controller. Step 5: Wire Up and Test the Direction Controller. Step 6: It’s DONE! 36 Comments.
How do you accelerate a stepper motor?
To accelerate a stepper from a starting speed to a desired target speed, the current speed just needs to be changed at periodic intervals. Most engineers use microcontrollers to achieve stepper control.
What is pulse width modulation PWM?
Pulse width modulation (PWM) is a modulation technique that generates variable-width pulses to represent the amplitude of an analog input signal. The output switching transistor is on more of the time for a high-amplitude signal and off more of the time for a low-amplitude signal.
How does duty cycle affect stepper motor?
If the microcontroller detects a change in the value of the duty cycle, it moves the stepper to the required position. Each time the duty cycle varies, channels are strictly toggled in a specific sequence: In Table 1 are values that obtain the step by step movement of the stepper motor.
Does microstepping increase speed?
Microstepping decreases the size of these increments, and increases their frequency for a given rotation rate. This results in significantly smoother low speed operation.
Why do potentiometers have 3 pins?
A 3 terminal pot used with 3 terminals, is basically just a voltage divider. As you move the wiper, you increase one resistor in the voltage divider, while decreasing the resistance in the other. So a 3 terminal pot is a variable voltage divider.
What is the difference between a and B potentiometers?
What is supposed to designated to A and what to B please ? The general convention for pots is that A is an audio/log taper and B is linear. For smooth control of volume, you should always use an A type audio/log taper pot. Using a linear pot here will give a very sudden volume reduction when going from 10 to 9.
Why do we need ULN2003 in driving relay?
Explanation: We need a ULN2803 for driving a relay because the relay coil requires 10mA or more current to be energized. If microcontroller pins are not able to provide sufficient current to drive relays then we need ULN2803 for driving relays. 4.
Why do we need driver for stepper motor?
A Stepper Motor Driver is the driver circuit that enables the stepper motor to function the way it does. For example, stepper motors require sufficient and controlled energy for phases in a precise sequence. Due to this, stepper motors are considered more advanced than the typical DC motor.
What is the working principle of stepper motor?
The basic working principle of the stepper motor is the following: By energizing one or more of the stator phases, a magnetic field is generated by the current flowing in the coil and the rotor aligns with this field.
What is step sequence in stepper motor?
In the full step sequence, two coils are energized at the same time and motor shaft rotates. The order in which coils has to be energized is given in the table below. Full Step Sequence. ►Half Step Sequence. In Half mode step sequence, motor step angle reduces to half the angle in full mode.
Terimakasih telah membaca How To Contro Motor Stepper With Uln 2003, semoga jawaban dari pertanyaan anda telah saya jawab semua. Semoga bermanfaat!